We’re with you all the way
We understand the importance of our customers’ needs and adopt the philosophy of developing close relationships by providing excellent customer service to support you every step of the way. We want to make sure that you get exactly what you need, when you need it.
Consultation
By sharing our technical expertise, we can help ensure a smooth production process from start to finish.
Tool Development
A small change here or there can make a huge difference to performance, quality or cost efficiency.
Find out more
Aftersales Support
Not getting the results you were expecting? We’ll go back to the drawing board with you for tweaking.
Find out more
Through analysing your set up, manufacturing processes and tooling knowledge, we can assist in eliminating the daily problems you face.
We offer consultancy packages if you would like our engineers to contribute to one of your projects with an on-site visit. To find out how we may be able to help, please get in touch.
We can:
- Provide additional engineering knowledge during initial design stages
- Share our technical expertise, so you can make the best design choices
- Suggest ways to keep costs down and reduce manufacturing costs by looking at quantities
New materials, manufacturing techniques and product developments are redefining our industry. We can help ensure that you’re using the best resources available for your tooling needs.
We can help you to:
- Develop a longer lasting tool
- Cut machine downtime
- Help you to utilise the potential of the latest materials on the market based on your tooling requirements
Once you have received your goods, we will continue to work with you to ensure they meet your requirements.
If a tool isn’t performing the way you were expecting, we’re here to help you take it back to the drawing board and help tweak the design for future production.
We can:
- Carry out analyses on worn or damaged tooling
- Offer suggestions for ways to improve tool life
- Provide continued support via your dedicated Account Manager to ensure complete customer satisfaction
Consultation
By sharing our technical expertise, we can help ensure a smooth production process from start to finish. Find out more
We offer consultancy packages if you would like our engineers to contribute to one of your projects with an on-site visit. To find out how we may be able to help, please get in touch.
- Provide additional engineering knowledge during initial design stages
- Share our technical expertise, so you can make the best design choices
- Suggest ways to keep costs down and reduce manufacturing costs by looking at quantities
Tool Development
A small change here or there can make a huge difference to performance, quality or cost efficiency. Find out more
- Develop a longer lasting tool
- Cut machine downtime
- Help you to utilise the potential of the latest materials on the market based on your tooling requirements
Aftersales Support
Not getting the results you were expecting? We’ll go back to the drawing board with you for tweaking. Find out more
If a tool isn’t performing the way you were expecting, we’re here to help you take it back to the drawing board and help tweak the design for future production.
- Carry out analyses on worn or damaged tooling
- Offer suggestions for ways to improve tool life
- Provide continued support via your dedicated Account Manager to ensure complete customer satisfaction
tailored to you
We provide a dedicated and customised service to each and every one of our customers.
We do this through the use of our bespoke software which provides accurate data in order to support day-to-day planning and ensure that we can meet deadlines and keep our promises to customers.
We provide:
- All customers with a personal Account Manager to ensure continuity of rapport
- Foreign language speakers for clear communication
- A weekly Open Order Book (OOB) for customers to manage expected deliveries
- Flexibility with lead times using our express service
- On-time delivery based on individual customer criteria
Our Capabilities
Over the years, UK Dies has developed a unique set of skills and capabilities that allows us to rely on a deeper technical knowledge of the industry and market.
We have the capability to machine a variety of materials from tungsten carbide in grades G2 to G6 and all grades of tool steels including sintered to M2 and hot work H13.
We have an ever-growing portfolio of over 100 specialised machines including CNC milling, CNC grinding, CNC turning and EDM. For a more detailed machine list, please do not hesitate to get in touch.
We pride ourselves on having a proven track record with our existing customers to provide high-volume production with a guarantee of consistent quality thanks to our bespoke machinery after CNC investment.
We have the accuracy and expertise to typically, but not exclusively, work to tolerances of 3 microns and dimensions of 0.6mm – 120mm standard (internal) and 1mm – 250mm (external). For other specifications and sizes, please contact us for a quotation.
Our products may be supplied uncoated or coated according to customer requirements with expert advice available regarding the most suitable options depending on tool use.
We hold a comprehensive range of carbide and steel materials for urgent requirements and can accommodate consignment stock/Kanbans to offer 100% product availability.
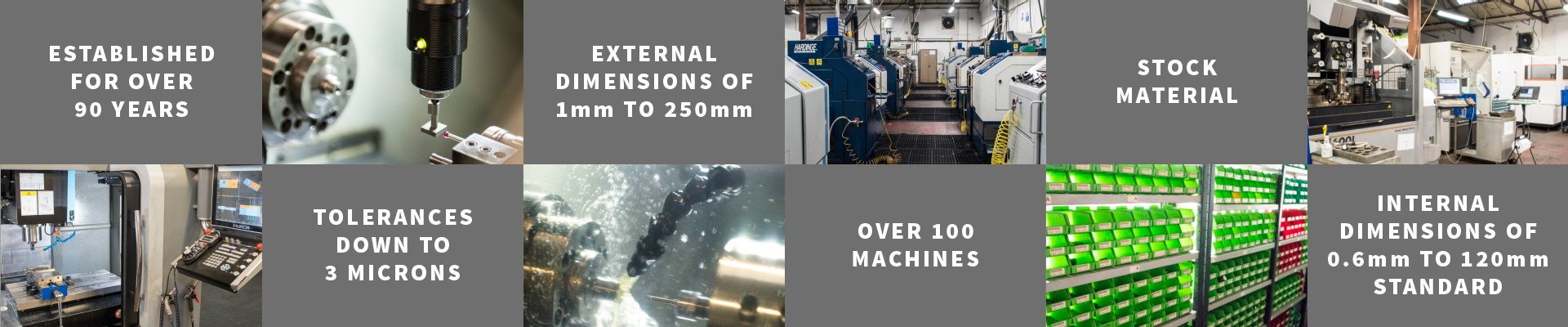